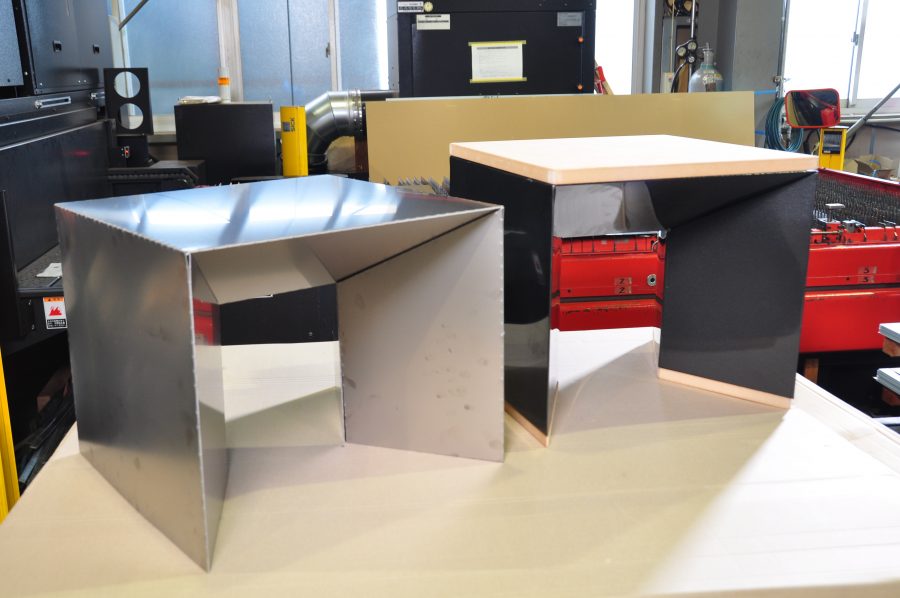
A decision to produce a chair from a single board was made. But what material would the board be? “Conventional materials are no longer appealing when it comes to designing chairs for the future. Titanium is the best,” declared Saito without hesitation. Titanium is a material that is also used in smartphones, and although it is expensive, it is lightweight and durable. It is also utilized in medical equipment, because it is less likely to trigger metal allergies. Given how many people will be seated at the Expo site, this is a crucial consideration. Instead of painting the chairs, the team decided to use a technique called oxidation-based coloring, which gives color to the metal. A color change is also more easily accomplished with titanium.
However, the hard titanium must be folded like origami paper to create the chair’s shape. The team chose to use laser processing to make rows of tiny holes in the sections that needed to be folded, utilizing the technology of the partner company Kumakura Shirring. The chair’s final shape is created by folding along the lines, and the folded sections are subsequently metal-welded to add strength. The production of a chair entails a number of processes, including material procurement, material research, design, sheet metal processing, welding, painting, coloring, and surface treatment, in which Dots and Lines serves as a starting point and then unites the efforts of eight companies in Tsubame-Sanjo. A prototype has been finished, but the metal has not yet been colored through oxidation. The team is still battling over details down to fractions of a millimeter, such as ease of bending, strength and balance when sitting on, thickness, and depth of folds.
According to Saito, it has been somewhat disappointing that Tsubame-Sanjo has been actively working on open factories for the past 12 years, but there was no horizontal connection. “We intend to arrange an experience-based event of sauntering in Tsubame-Sanjo during the Expo, showing guests around the town’s small manufacturing factories. To entice people to visit Tsubame-Sanjo, we are considering creating miniature versions of the chairs we will provide for the Expo site. We intend to have visitors tour every factory that is involved in the process needed to finish the project, rather than just one factory workshop. The participants will be required to complete the work for each process themselves in addition to touring each factory. We are thinking of designing a tour that would enable visitors to Tsubame-Sanjo to progressively finish the chairs,” emphasizes Saito. “We want people to take advantage of this manufacturing experience as a chance to tour the town and get to know it.”
“Even with current technology, a very small amount of blanking material is produced when creating the folds. That is why our project has a ‘production yield of 99%.’ We want to somehow eliminate the remaining 1% and aim for 100%. Through the Co-Design Challenge, we hope that as many people as possible from around the world will sit on the chairs and visit Tsubame-Sanjo,” hopes Saito. He wants the town of Tsubame-Sanjo and its technological prowess to be known throughout the world. Saito is looking forward to achieving his dream of “making Tsubame-Sanjo the world’s number one manufacturing town.”
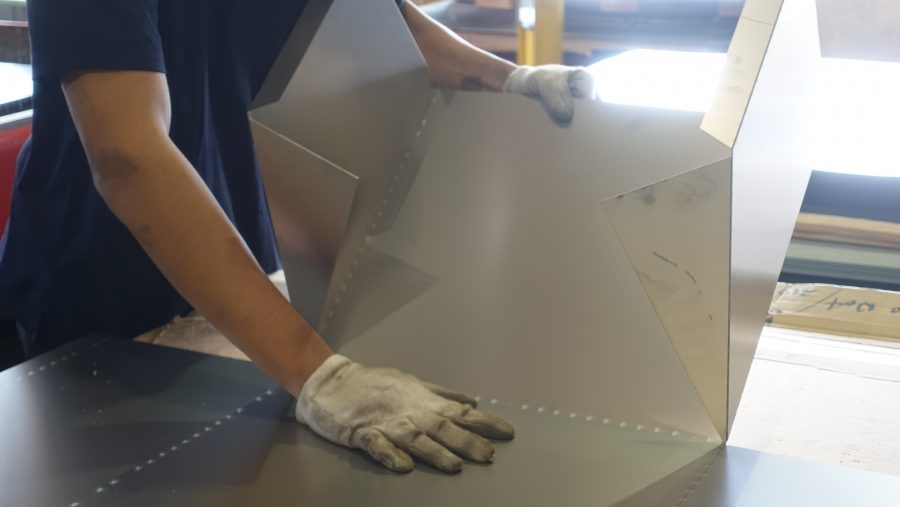
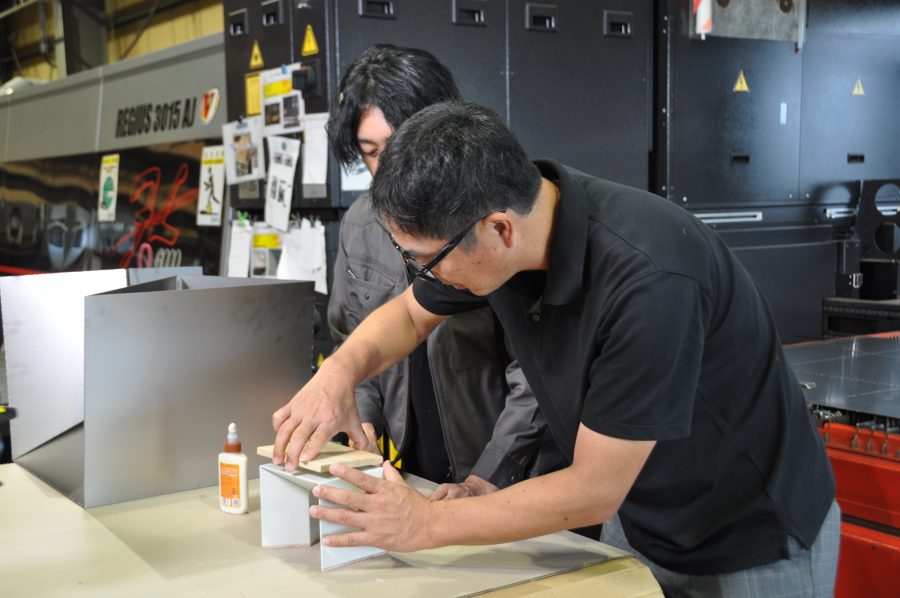
Share this article