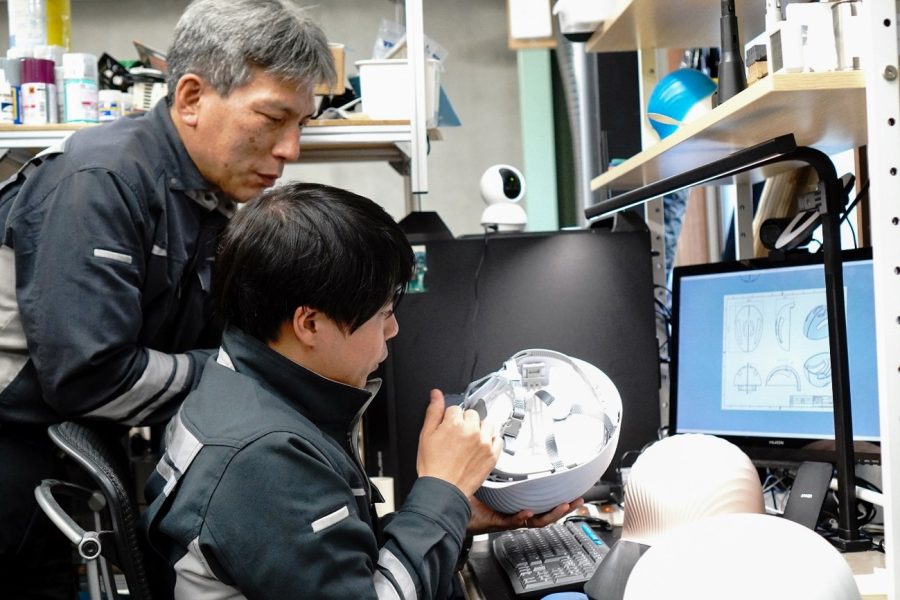
Ever since the holding of the Expo 2025 Osaka, Kansai, Japan was determined, Nambara has been looking for an opportunity to participate. He wanted to show the manufacturing technology of Japan’s small factories to the world. Koushi Chemical Industry was found by his grandfather in 1969, and succeeded by his father, who worked hard to preserve the company based on the strength of small-quantity, multi-type production. After graduating from the university, Nambara once worked for a major general contractor. He was involved in large-scale construction projects such as hotel and tunnel construction. When he turned 30, he made a big decision not to leave the company as it was and switched jobs in 2019.
But the start was gloomy. He was disregarded when he visited an exhibition, just because the company indicated in his business card changed from a large-sized company to a small/medium-sized one. Nobody even listened to him when he offered a business meeting. The company certainly existed, but it was like an invisible one. He lost a vision as to where he should go.
At that time, he learned about a project by Osaka University to send face shields, which were in serious short supply, to medical institutions. The world was in the midst of the coronavirus pandemic. He offered his cooperation, saying, “We can manufacture products for mass production of frames.” When the company raised funds through crowdfunding, it got more than five times its target amount, and some people even went out of their way to send the benefits they received from the government to the company.
Being touched by the overflowing goodwill in the world, his passion for manufacturing, which he had always loved, was revived. He is now using his skills to help solve social issues. It may sound cookie-cutter. But, the motive for doing so deserved a nod.
Around the time when the prototype of SHELLMET was completed, he found a clue to the Expo in the email newsletter from Higashiosaka City. It was an article for promoting the participation in the Co-Design Challenge. He thought that this was the only way. A number of inquiries have already been made by foreign companies that have taken notice of SHELLMET’s materials. A Spanish manufacturer of clothing and sundries also placed an order for the product. It has won a gold award in the design category at one of the world’s largest international advertising festivals, and has also received inquiries from overseas exhibitions on the environmental theme. It’s an unimaginable response.
In the area surrounding Nambara’s company, there are many small and medium-sized companies that support people’s daily lives with niche technologies that the big companies do not target. They have held on for 20 years, unable to realize price pass-through of the higher cost of raw materials for their prices. “Every company has its own advantages. It’s just that they haven’t found the right way to showcase them or flourish in the right areas. I hope that our small endeavor will lead to the revitalization of all the factories in the town,” emphasizes Nambara.
Nambara now feels great joy when he is able to take on the challenge of manufacturing every day.
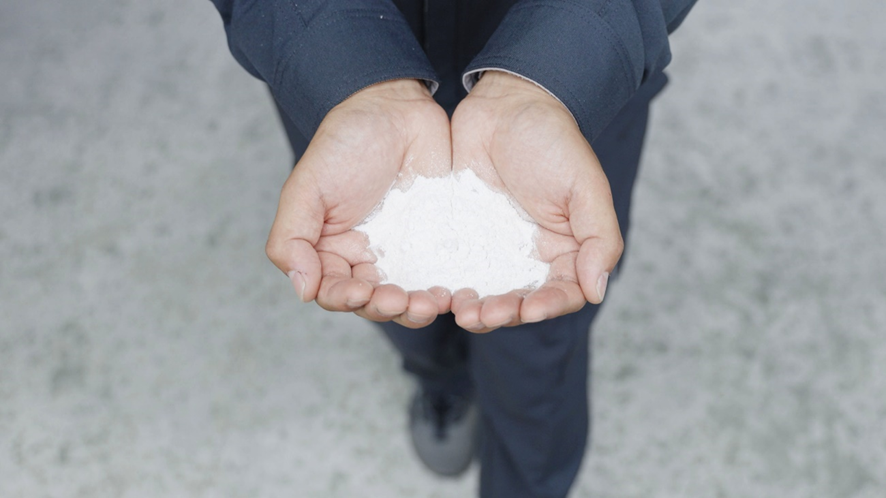
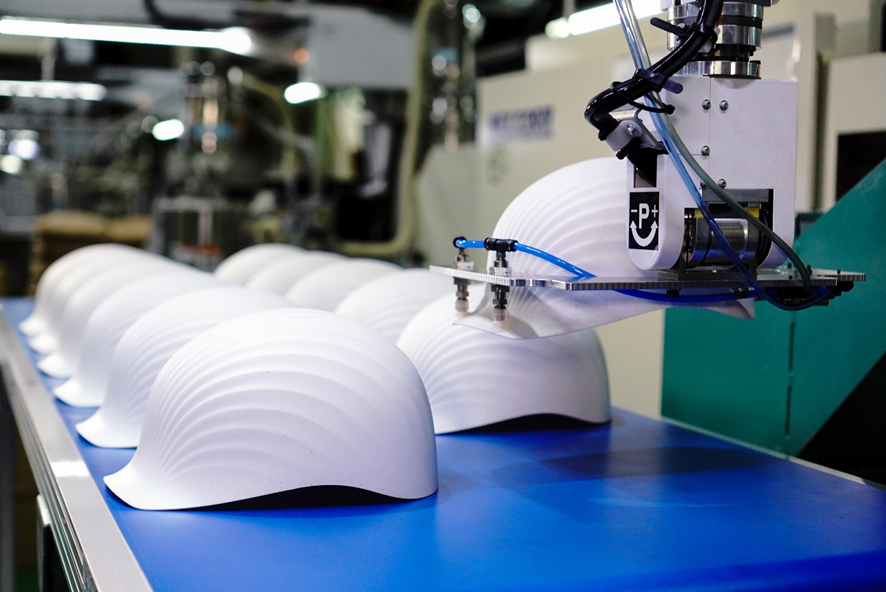
Share this article