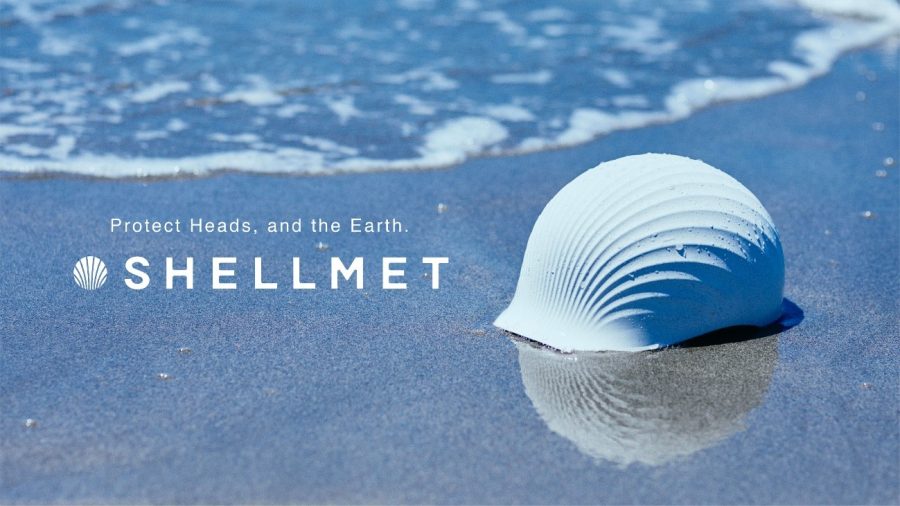
“SHELLMET,” made from scallop shells that have nowhere to go, will be adopted as one of the official anti-disaster helmets for the Expo 2025 Osaka, Kansai, Japan. The endeavor to produce it was made by “Koushi Chemical Industry,” a plastic processing company headquartered in Osaka City, Osaka Prefecture, with a production base in Higashiosaka City. Behind the endeavor was a single-minded desire to demonstrate the potential of manufacturing at a small factory and to solve social problems.
In the winter of 2021, a comment of Tetsuya Nambara, Head of Planning and Development Department, created more buzz on social media than ever. His tweet about eco-plastics molded from eggshells was spread and it received many messages. One of them caught his attention. A large surplus of scallop shells in scallop-producing regions in Hokkaido has become a problem. Nambara suddenly thought, “Shells are also made of calcium carbonate, the same ingredient as eggshells. By utilizing our own processing technology, we may be able to breathe a new life into shells that are of no use, and play a role in solving the problem.”
Once you have an idea, you have to act. He contacted Sarufutsu Village in Hokkaido, which accounts for 10% of the total volume of landings in Japan, and visited the town office. When guided to the fishing port, he was speechless at the unexpectedly large number of piles of shells lying in the open, beside the fish processing plant. Approximately 40,000 tons of shells are discarded annually in the Soya region, including the village. The village was concerned about foul odors and soil contamination, and was seeking countermeasures, but has not been able to find a sustainable way, which has been a longstanding issue.
He met with Mayor Koichi Ito and gave an impassioned speech about his idea on eco-materials made from a mixture of shells and waste plastic. Perhaps sensing the seriousness in Nambara, Ito’s voice bounced. “Finally, someone who wants to take on the challenge has appeared,” he said. Nambara made a firm determination at that time. The day after his arrival, he spent a day boiling and sterilizing about 300 kg of shells.
Upon returning to Osaka, he began his experiments. The shells were crushed and mixed with various types of waste plastic to check the compatibility. The number of patterns tried exceeded 100, including the fineness and quantity of the crushed grains, and mixing methods. He repeated the experiment at home, even in the early hours of the morning and late at night, in between his regular work duties. His natural love for manufacturing made him excited, and he was absolutely thrilled.
At the same time, he pondered what kinds of products could be created with this material. Japan suffers many disasters, so he decided to make a disaster prevention tool. From the shell’s role in protection against foreign enemies, a helmet came to his mind. The surface is corrugated, making the design instantly recognizable as a seashell. The completed prototype has the effect of reducing CO2 emissions by 36% at a maximum compared to when only ordinary plastic materials are used. It also successfully increased strength by 33%. The name “SHELLMET” was chosen.
When Nambara reported the results to Mayor Ito and others, they were surprised and pleased, saying, “I can’t believe you actually have found a solution,” and “This is amazing.” In December 2022, about a year after the idea was conceived, the company began pre-order sale through crowdfunding, and watched the progress with great excitement. The result was a flood of applications, far exceeding the target amount. The response came from overseas as well.
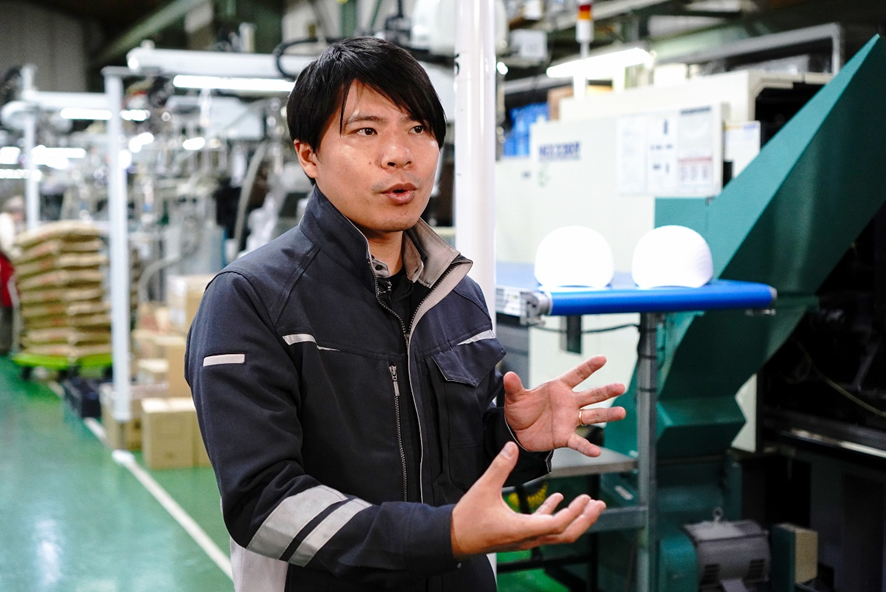
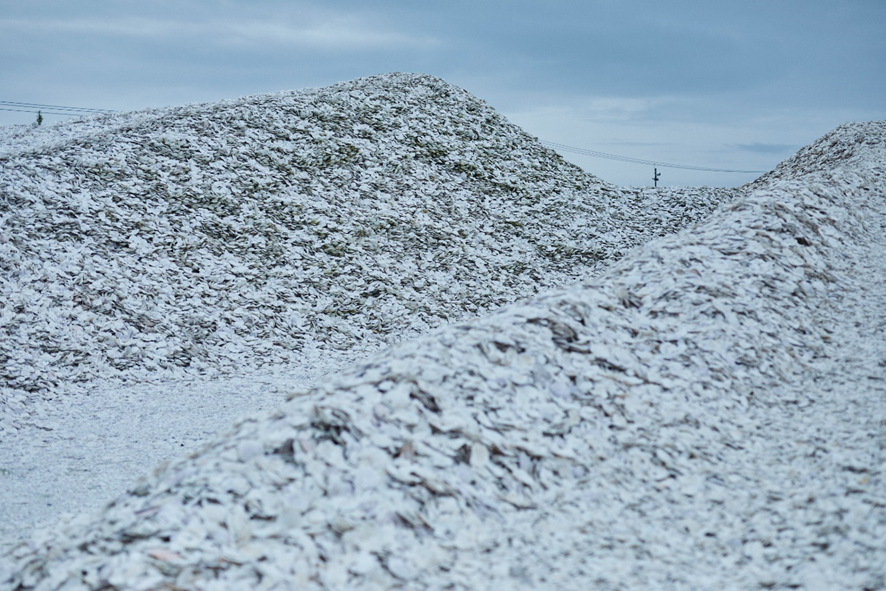
Share this article