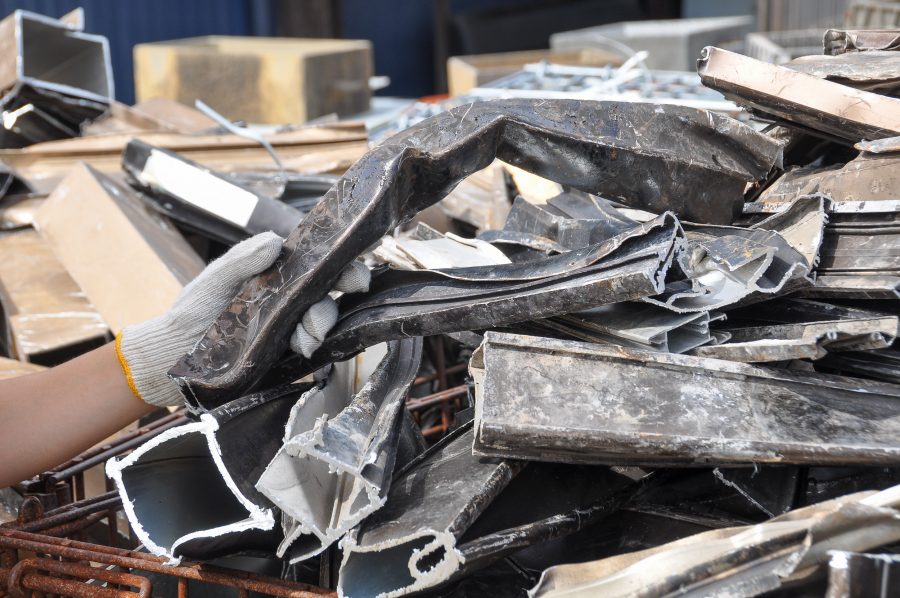
The amount of disaster waste resulting from the 2024 Noto Peninsula Earthquake is estimated at 2.4 million tons. Ishikawa Prefecture has announced that it will utilize approximately 1.2 million tons of recyclable disaster waste, such as metal (about 20,000 tons) and concrete, as materials for reconstructing the damaged areas.
This has changed what Kanamori Alloy pursues in the Co-Design Challenge from effective utilization of local waste materials in sign stands to effective use of disaster waste. Koge took swift action. She searched for the route through which disaster waste was collected, but could not find any official destination at which disaster waste arrived. While it took Kanamori Alloy about three months to finally find a place where waste materials were gathered, it collected 200 kg of nonferrous metals, including aluminum sashes. The screws of the collected aluminum sashes used as window frames were removed one by one by hand. While saying with all her heart and soul, “We would like to create sign stands that will lead to future generations by using waste metals that served people in their daily lives as materials together with the memories they hold so that the people in the Noto region can live positively again,” Koge is bothered by the fact that “the process of collecting waste materials is updated every time a disaster occurs, but information on where collected disaster wastes were brought, where to contact for inquiries, and any other related matters has not been shared thoroughly or accurately.” She also said that she would strive to come up with solutions to the issue of effectively using disaster materials as swiftly as possible through the program.
Koge was born to the Kanamori family as the elder of two sisters. Women were not allowed to work in the casting industry that handles flames, and Koge had never been told by her grandfather or father to take over the business. However, a concern about the future of the family business had always been in the back of her head. After graduating from a university in Tokyo and working at an advertising agency for seven years, she moved to an overseas country for her husband’s job. As she came back to Japan, she decided to jump into the casting industry, thinking that it would be now or never.
Koge added words on behalf of metal that is austere and silent, saying, “We produce about 1,000 kinds of products in small quantities each year with some products being ordered only once every 30 years. We started with adopting visual control methods to our analog factory operations. We then launched KAMAHACHI, a Business-to-Consumer lifestyle brand, while reviewing and identifying our company’s strengths. Our company is just one of the small- and medium-sized companies that are said to account for 99.7% of all the companies in Japan, but we believe our mission is to pass down the techniques and tradition that we have developed and it is important to share them in other fields than the Business-to-Business one in order to accomplish the mission.”
Kanamori Alloy considers offering visitors opportunities to experience the casting process at its head factory during the Expo 2025 with the aim of sharing its recycling-oriented manufacturing. “We are making several plans, such as an event in which visitors can create sand molds with the assistance of our craftsmen and pour aluminum alloy smelt right there to make their own kashikiri dessert forks, one of the tools used for cutting and eating Japanese traditional confectionery, and an event that allows them to enjoy food using what they have just created. We would like to encourage people to think about metal’s ecosystem together with us,” she hopes. Nothing can stop Koge from expressing her love and passion for casting.
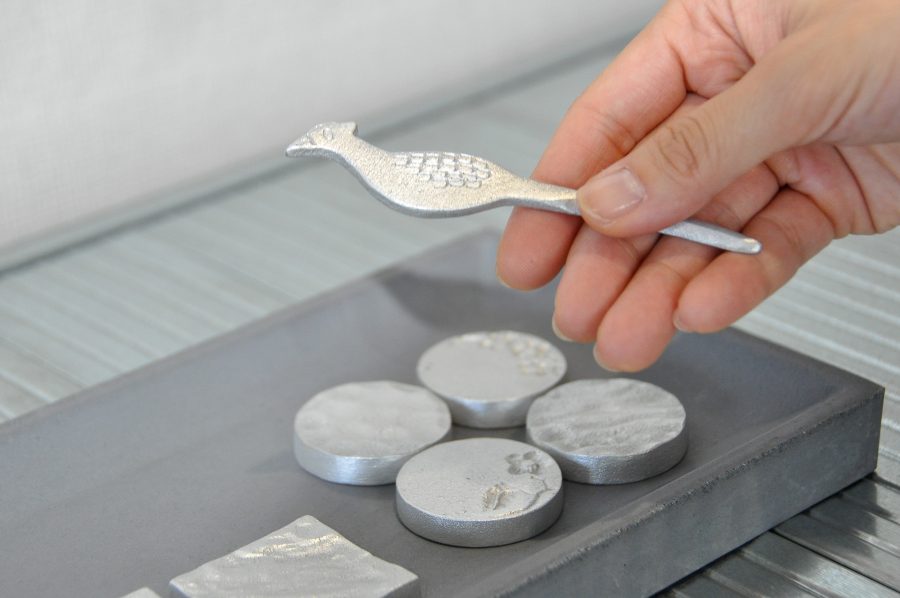
(aluminum casting/design: pheasant)
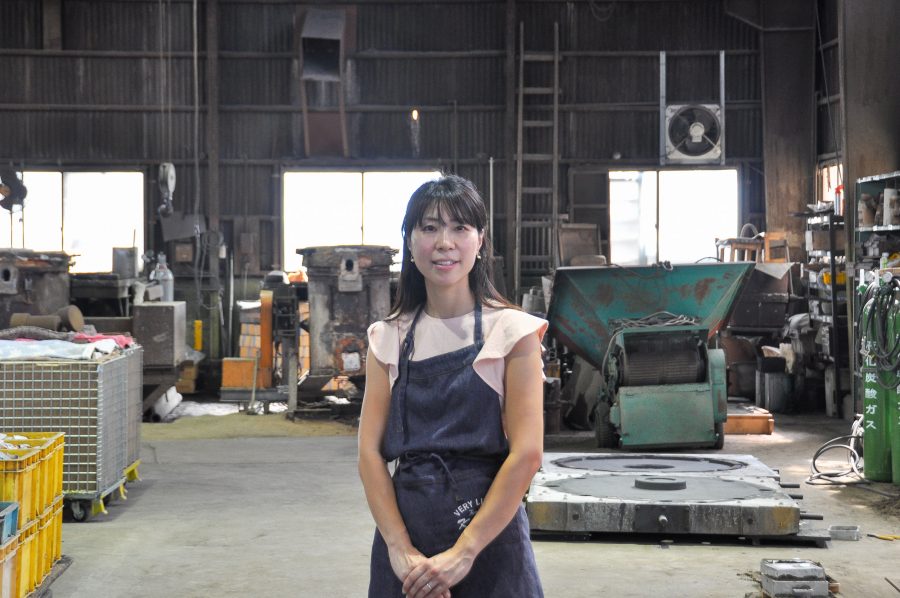
Share this article